3D Printing is the process of using a 3D Printer machine to fabricate a 3D Model, which is a convenient and fast method of production, and much more accurate compared to manual work.
3D Printing in SP Fablab requires certification, which is given after succesfully completing a quiz, requiring you to score 100% to pass. However, after completing this, you will qualify to be able to book for the practical test. Aside from hardware, you will also need to download the slicer softwar to prepare your model for printing, which in our case, is Cura In my case, I will be installing Ultimaker Cura 4.6 for my use.
The school's fablab has 3 types of 3D Printers as of the time of this documentation. The 3 types of printers are:
Cura is used as it can be changed to prep a model for all 3 types of printers. The software can be installed by clicking on this link to navigate to the website.
Shown below is a quick start guide for Cura
The 3D Printers can do a few manufacturing processes, which are methods of creating or making something. In this case, the specific manufacturing processes the 3D Printers can do are:
- Additive and Subtractive Manufacturing, which is essentially refer to the addition and removal of materials to a product.
- Cutting, which refers to the seperation or opening of an object into multiple pieces
- Forming, which can be boiled down to reshaping or manipulating an object and its shape, without removing or adding any additional material.
But why would you use 3D Printing?
While 3D Printing may seem like an interesting thing to learn, what reasons are there to use it outside of pure leisure or personal interests? What advantages and motivations would there be to use this method of manufaturing a product?
- Design Freedom
- This is a large reason for many people, as 3D Printing can be done from a 3D Model, allowing many people to simply pick up their laptop and download a 3D design software and design a model to their wishes, which can then be printed out easily, without needing to worry about their personal handicraft skills.
- Faster Production
- For large projects with many components, 3D Printing can be much faster to produce and make as compared to manual processes, saving much more time for people to work on improving the project or design further by moving onto testing a physical prototype.
- Customisation
- The model, as mentioned before, is digital and can be accessed and worked on easily from the comfort of your laptop or desktop, allowing you to customize and change things on the fly if the printed product is not to your liking, instead of having to physically modify the product and risk not being able to revert the changes made.
- Less Waste
- Due to the nature of 3D Printing, you can save materials by making slight tweaks to thick planes of a product, or simply just not having to remove large pieces of materials to create the shape you wish to see.
- Many other Reasons
The creation of this useful process can be attributed to many people over the years, but some notable names are:
Of all the advantages 3D Printing presents, one particular advantage is the large range of materials that can be used when printing out a design. These materials are:
- PLA
- Polylatic Acid, or more commonly known as PLA, is a default filament for most extrusion 3D printers, and one of the most popular as it is rigid, but does not require high temperatures, while still being low cost and has good shelf life.
- ABS
- Acrylonitrile Butadiene Styrene, or ABS for short is a low cost plastic that is heat resistant, impact resistant, and rigid. It is commonly used to print cases and toys such as lego bricks.
- PETG
- Glycol Modified Polyethylene Terephthalate (PET), or PETG for short, is a chemically resistant, semi-rigid material that has good impact and water resistance. This is generally used in products that are in direct exposure to water such as Planter Pots, or Water Bottles.
- Nylon
- Nylon is a heat resistant plastic that is also known for its toughness and flexibility, but it requires temperatures as high as 250 degress celsius. It is used to print cable ties and other flexible palstic products.
- TPU
- Thermoplastic polyurethane, or TPU as it is better known by is a plastic that is elastic, transparent and also resistant to oil, grease and abrasion. It is mainly used in silicone, and mobile phone covers.
- HIPS
- High-Impact Polystyrene, or HIPS for short, is as its name implies, a high impact resistant material that is durable, and soluble. It can be used in DIY Projects or as a support materials for printing a project using a non soluble material.
- Glass
- Glass is a transparent material that can resistant some impact, albeit it is fragile and brittle. It can be used to print transparent pieces such as windows or viewing panels
- Ceramic
- Ceramics are heat resistant and hard wearing, but fragile. They are generally used visual arts, or in the manufacturing of tableware.
- Carbon Fiber
- Carbon Fibers are rigid materials that are strong and stiff due to it being a composite, all while still being lightweight. It does not require a heated bed to print. It is often used to make functional protoypes or lightweight props.
- Metals
- Aluminum, Steel, Titanium, etc. Metals in 3D Printing can be used to print much more durable parts that can withstand large amounts of mechanical stress, heat, and corrosion. These can be used to print parts in mechanical systems.
- Food
- Food can be 3D Printed using pureed ingredients, and are used in the production of food that are easier for people with chewing disabilities to eat.
- Concrete
- This requires a large 3D Printer, but it can be used to build structures quickly at low cost.
However, despite all these advantages, 3D Printing does not come without its problems and constraints. These constraints are things to keep in mind when designing something to be 3D printed.
- Failure
- When the design is not printed according to the model, it is considered a failure. This can stem from the temperature that the design is being printed at being too low, causing the layers to not stick and fuse like they are supposed to. This can also stem from the geometry and design of the model, so ensure that no ssections are too thin or small for it to properly fuse.
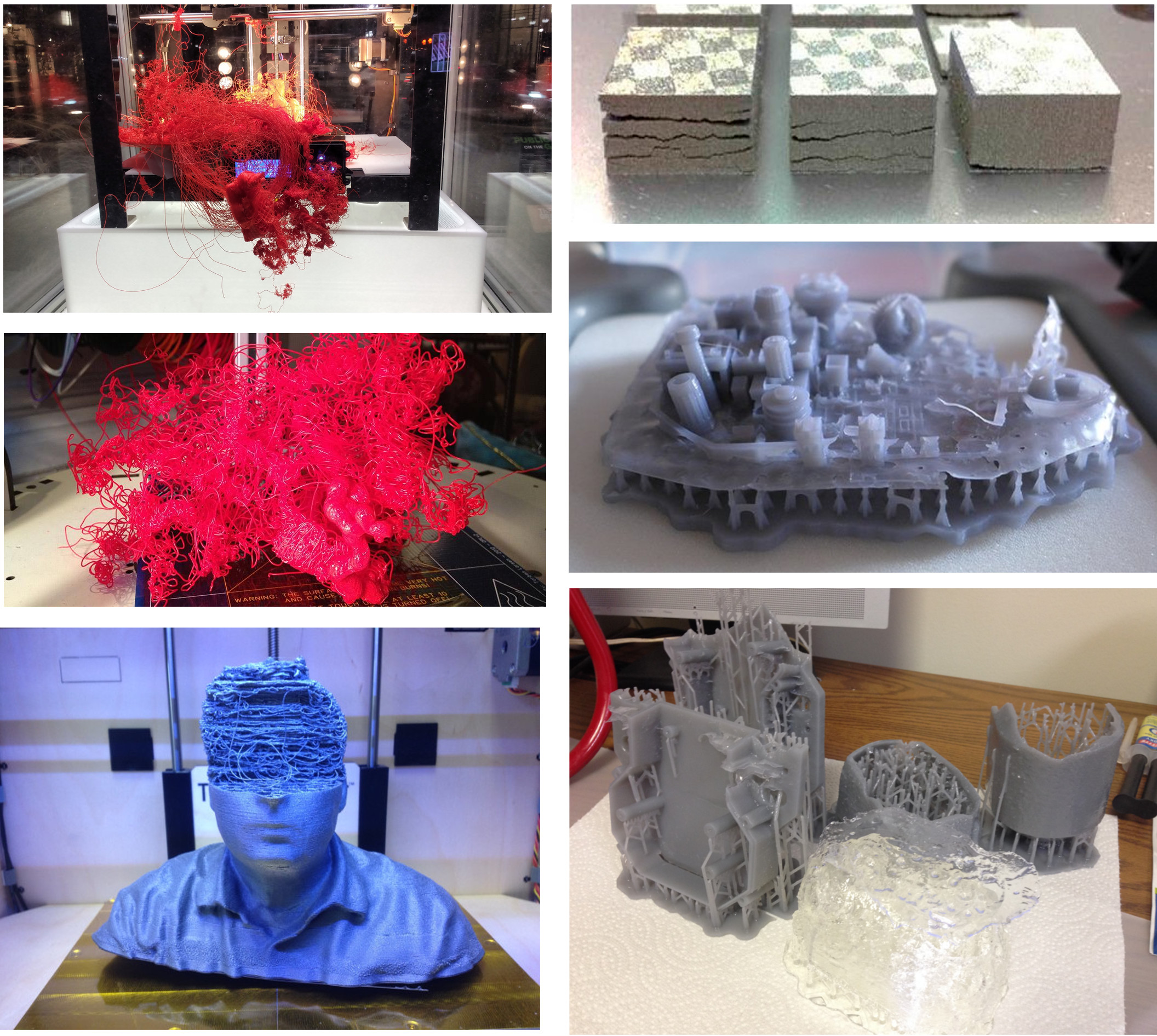
- Layer Height
- 3D models are printed in layers, and the height of each layer is aptly named the "Layer Height". This setting can be adjusted through a slicer program, and can affect the final print's speed, resolution, and smoothness. The height of each layer is typically measured in microns, with one micron being equal to 0.001mm. By lowering the layer height, the printer will print more in detail as it prints more layers to reach the desired height. Additionally, layer height may affect precision in smaller moving parts found in print in place mechanisms.
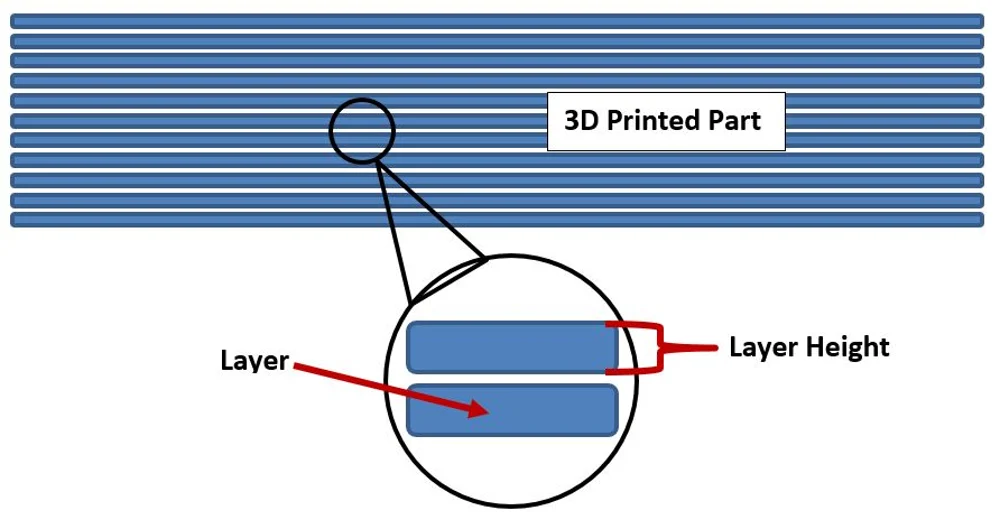
- Time
- The time taken to print can be a large constraint, as depending on the size or complexity of the print, it may take a long time to print.
- Cost
- The cost of the materials used to print can also play a big part, as you may require some materials for certain sections of your design. You also have to ensure that wasteful sections are removed to prevent waste of materials.
- Ventilation
- The process of 3D Printing can create some fumes emit some substances such as ultrafine particles which may cause damage to the human body. Hence, we need to ensure that there is sufficient ventilation when 3D Printing.
- Supported Overhang
- Overhangs at extreme angles need to be supported otherwise it will fail due to 3D printer limitations. Hence, there is a need to implement supports like the ones shown below.
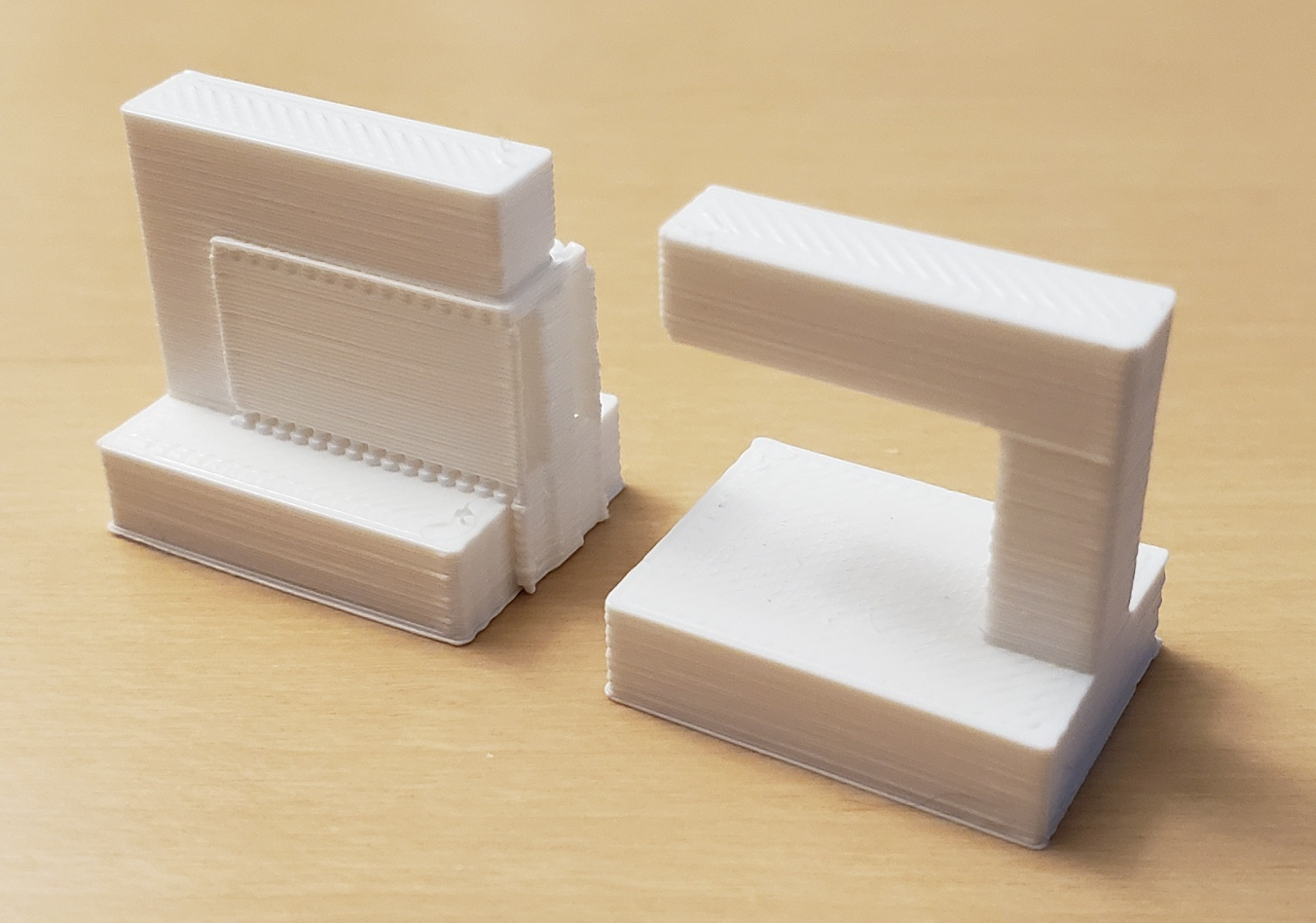
- Supported Clearance
- Clearance need supports in between to ensure that loose pieces do not fuse to the main body.
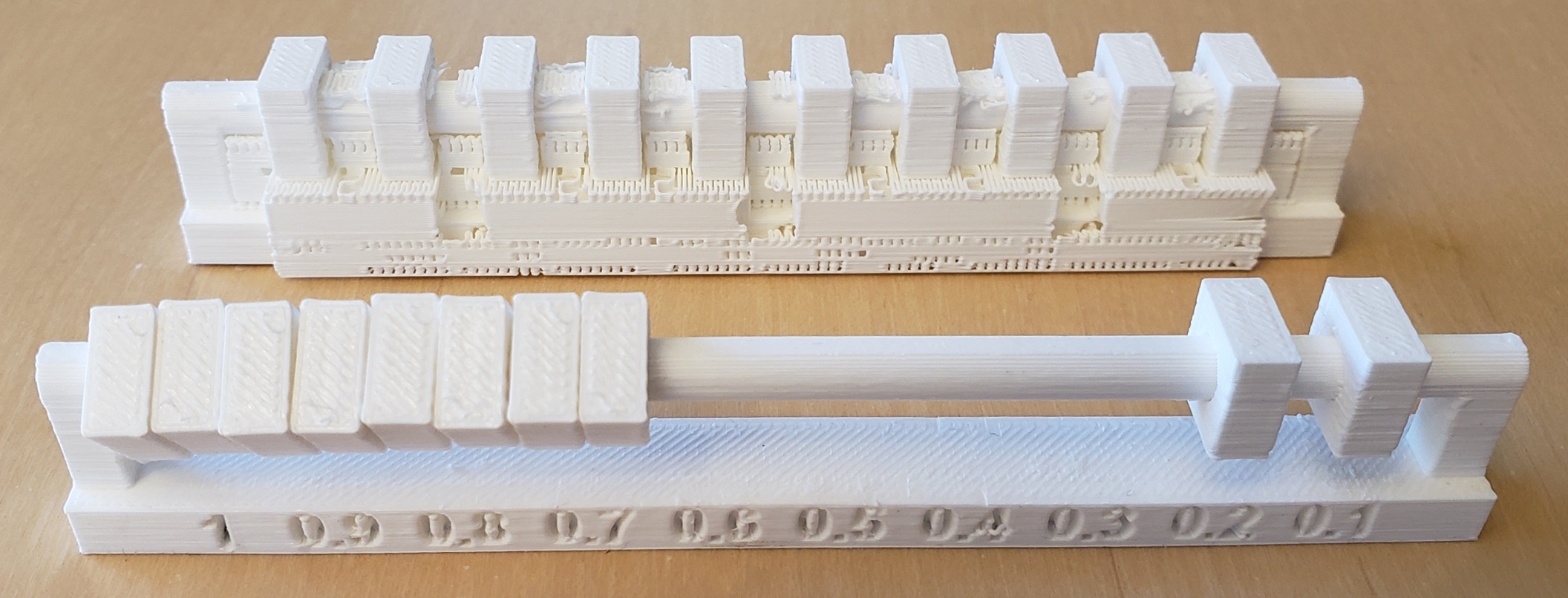
- Unsupported Overhang Angle
- Different 3D Printers can print different overhang angles without failure and hence it is important to test and experiment to verify what range of angles the printer you are using can print, otherwise this may lead to a print failure when the print collapses or is unable to print properly.
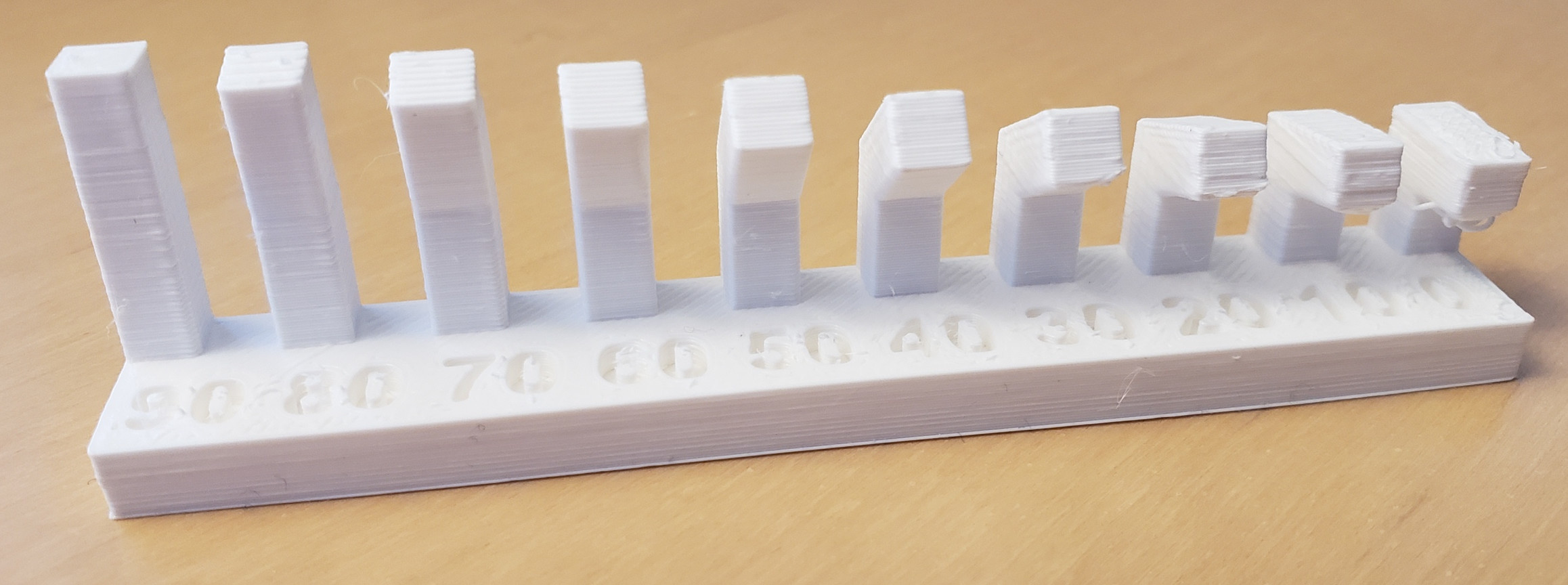
- Unsupported Bridging
- Different 3D Printers may be able to print bridging structures of different lengths without failure, and hence, it is important to test and experient to verify what lengths of bridging your printer is capable of.
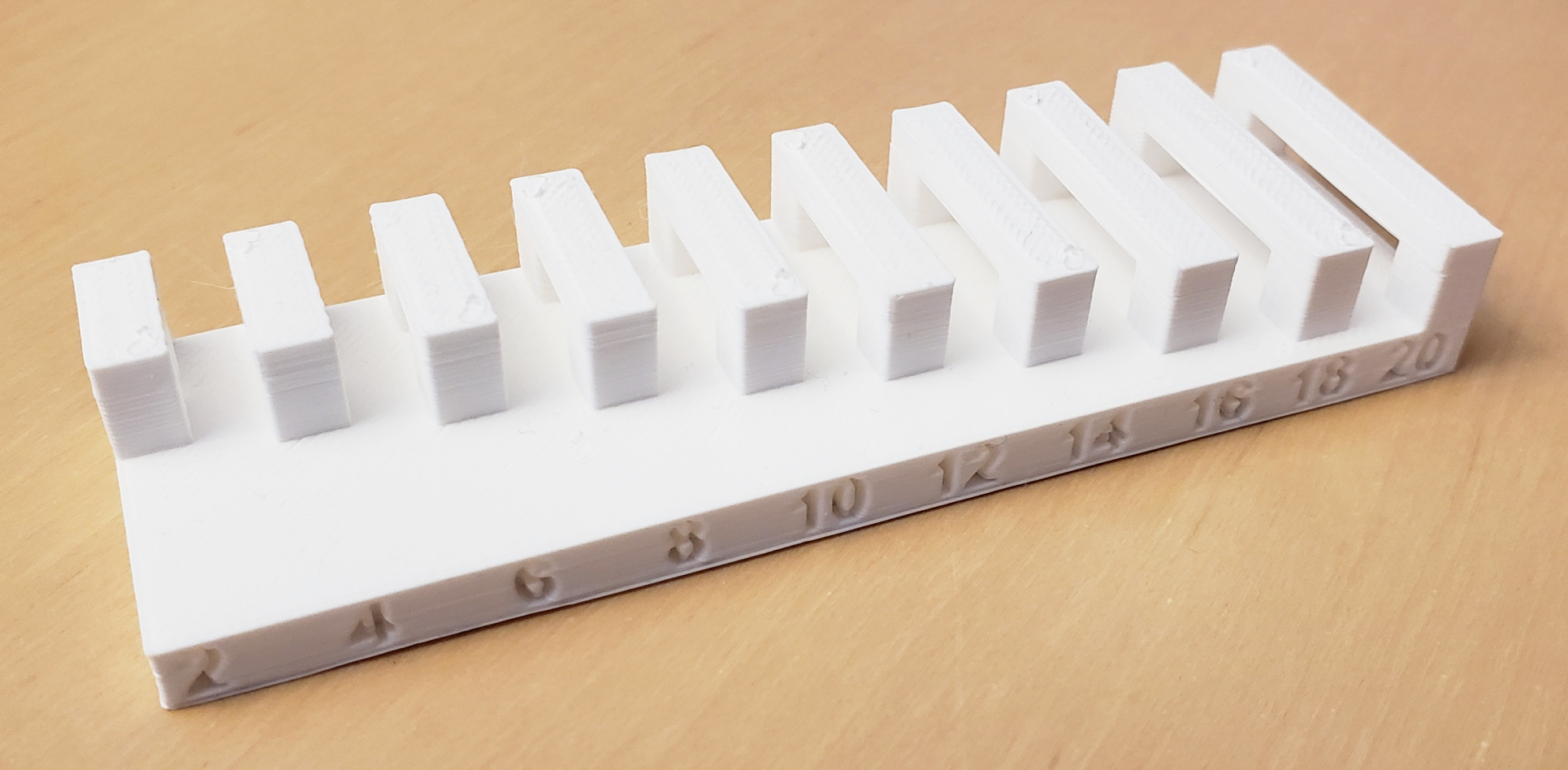
- Wall Thickness
- Wall Thickness is a variable that has to be controlled, as if it is too thick, it will waste time, money and material. However, using too little will lead to your printer being unable to properly print the model.
- Dimensions
- The dimensions of a project can greatly affect the time taken to print it and the resolution.
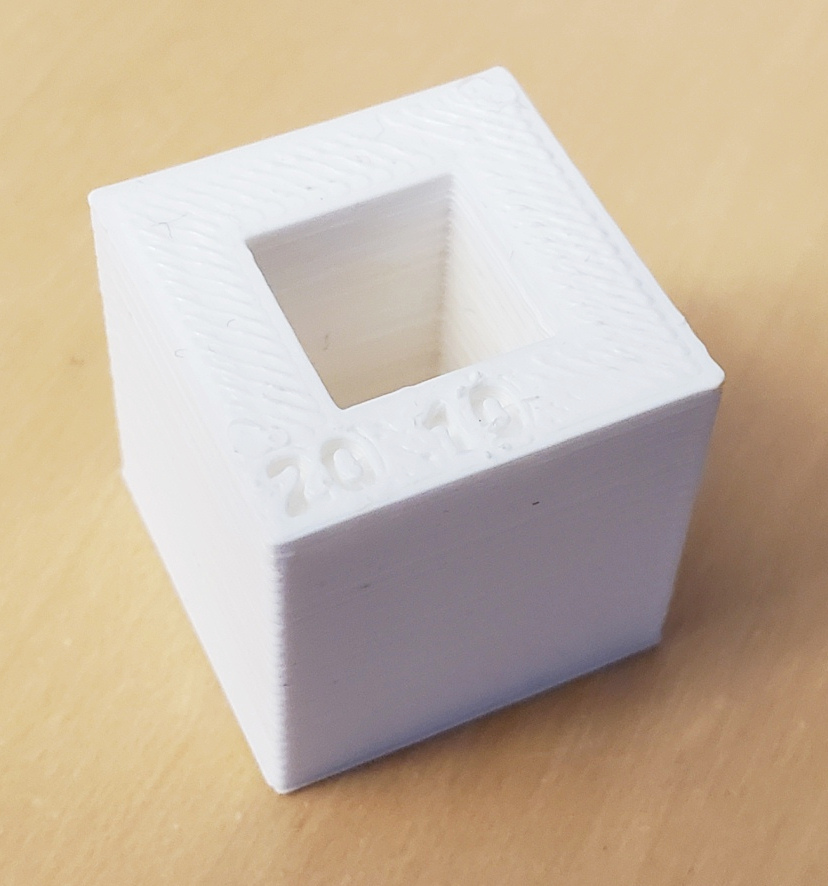
- Anisotropy
- Anisotropy is the property of materials when printed along a certain direction. Some materials may assume or have different properties when printed in different directions. This is important to take note of as some materials may be designed to withstand stress, but may need to be printed in a certain manner to carry out its desired purpose effectively.
- Surface Finish
- Infill
- Post-Processing
To test some of these afore mentioned constraints,
With this in mind, an ideal workflow should rememble something like this image shown below.
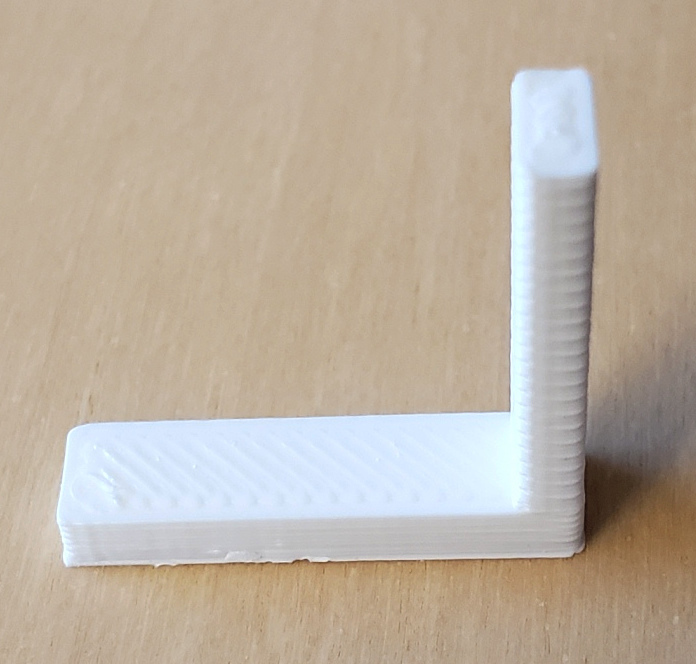
One way of testing the various constraints is to create models that demonstrate and test the limitations before failure occurs.
As shown below, I have created a model that can be used to test the clearance constraints of the 3D Printer.

You can find another 2 of my groupmates' models for other constraints at these links:
https://ian-low.github.io/EP1000/3dprint.html
https://mochidaisuki.github.io/Dfab-website/3D%20Printing.html